We know we are helping to make a product that helps this nation and helps build the world.
When it comes to cement, members from Local D194 (Chanute, Kansas) know a thing or two about the level of care, effort and excellence required to produce it. After all, it’s the central component in concrete, and it’s critical to important infrastructure: roads, homes, hospitals, schools, skyscrapers, dams, ports and more.
The Boilermakers at Ash Grove Cement aren’t just committed to producing an exceptional product—they’re also proud to be a part of building the world.
“It makes me excited to get up in the morning, to know I’m coming in here and making a difference,” says Boilermaker Mallory Guiot, a physical tester and analyst who evaluates cement at each stage of production to ensure Ash Grove clients receive a quality product.
“[Cement is] just vital to civilization,” says Tamara Leon, a materials handler.
According to L-D194 Vice President Russ Carlburg, the plant, located in Chanute, Kansas, has access to some of the region’s best limestone—which is the base for cement.
It’s very hard work, and it’s not for everybody. But those that choose to make a career out of it as Boilermakers, well, they’re cut from a different cloth.
“And we have a lot of it,” he says. “The guys and ladies are out here willing to go 110%. They take a lot of pride in doing the job and making sure the job is well done.”
The operation in Chanute is vast. They have a quarry where limestone is mined. The plant has maintenance crews, a lab to test quality, production crews, a massive kiln and even a railroad yard.
“We have locomotive operators, truck drivers, welders. We have electricians, we have mechanics—and they’re all in the Boilermaker union,” says L-D194 President Kenny Swiler.
Everything in the plant runs hard, so a huge maintenance force is required for tasks ranging from patching to welding, changing rotary feeders and more, including all upkeep on mobile equipment with motors and wheels.
“We make about 20 trips a day [to the quarry] which averages to about 160 miles a day, and we do about 6,000 tons on average a day,” says Cecil Gant, a quarry truck driver.
Ash Grove operates across the U.S. and in Canada and has a network of cement plants.
“Ash Grove is a family of very good cement plants, and we’re in good market locations,” says Stuart Tomlinson, an Ash Grove manufacturing vice president. “But the best part is our workforce. Having the Boilermakers on site makes us an efficient operation through having top-notch people who know what to do to make cement.”
And making cement takes precision.
“I don’t think the general public has the smallest clue what goes into making cement,” says repairman Jared Ranz.
First, limestone is hauled from the quarry and crushed enough to go into a cement dome, where it’s crushed into even smaller material. Then the crushed limestone is mixed with sand, shell, clay and iron ore. That mix goes into a raw mill, which grinds the mix. The in-plant lab runs tests on the mixture, and when it meets standards it’s sent to the pre-heater tower before being run through a kiln.
“Tests are run on cement for compressive strength, air permeabilities making sure the product we’re putting out is up to standards,” Guiot says.
As the kiln turns, it produces clinker, a kind of pebble. After the clinker cools, it travels to the finish mill for grinding. More raw materials are added and from there, after it reaches the correct temperature and passes more testing, it’s stored in silos to be shipped to customers.
“We all care about what we make here because that’s putting our name, Ash Grove, on the cement we’re shipping out,” says Marcell Seamster, a control room operator.
The Boilermakers at Ash Grove agree: They do their best job because they’re proud of what they make.
“Our product is the foundation of the world,” Swiler says. “There’s nothing that’s not set on cement. And that’s something to be proud of when you’re making something that goes everywhere.”
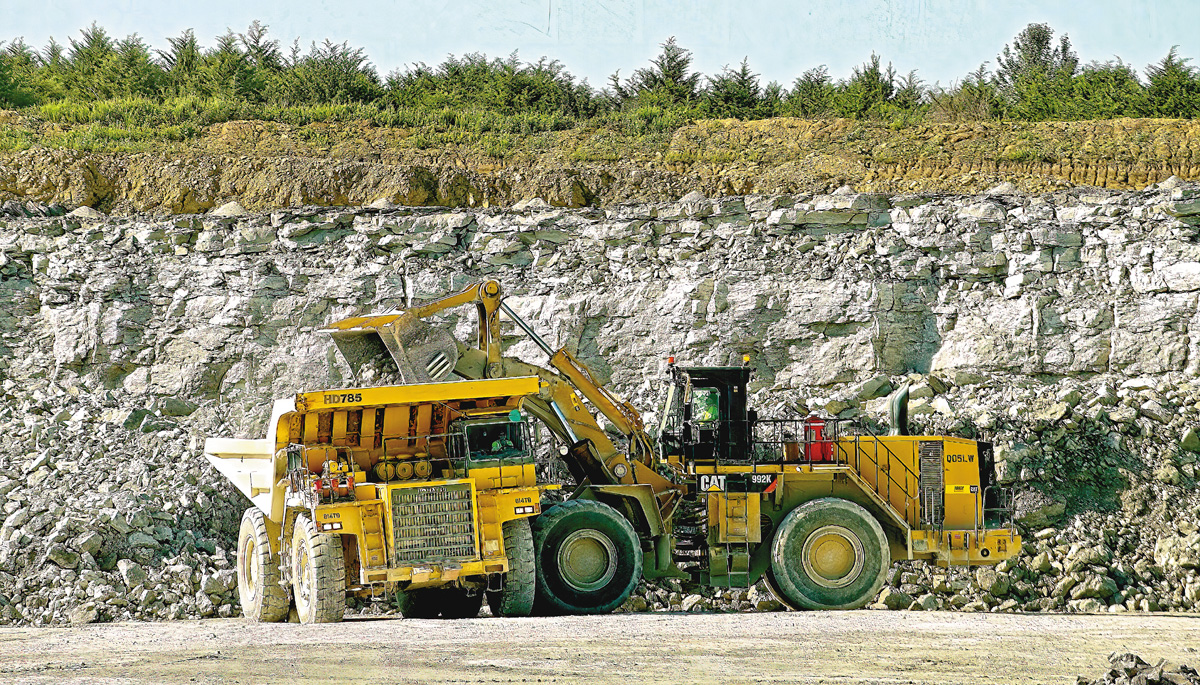
The Process of Making Cement
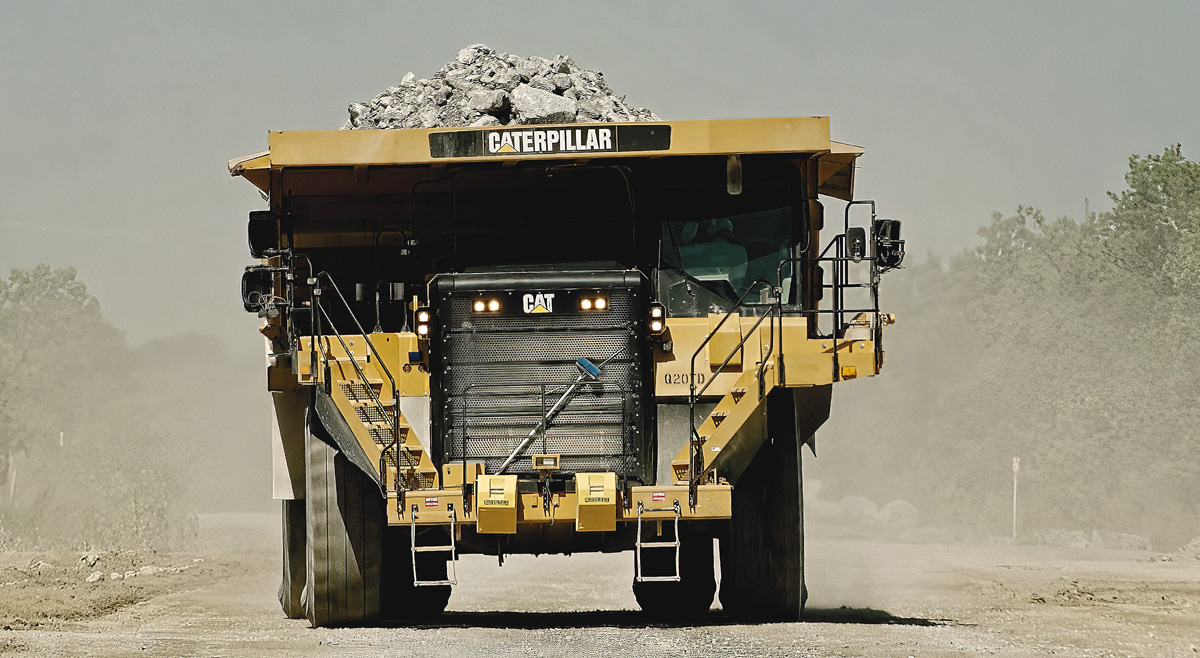
1
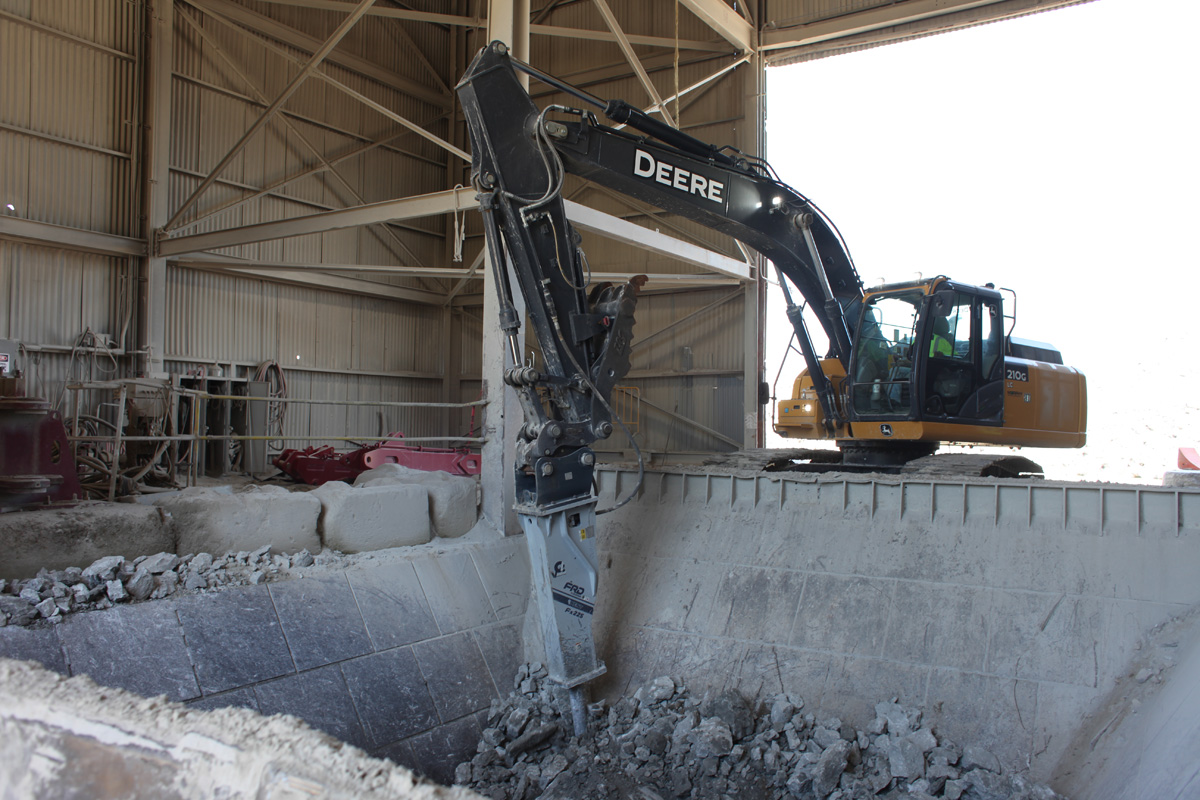
2
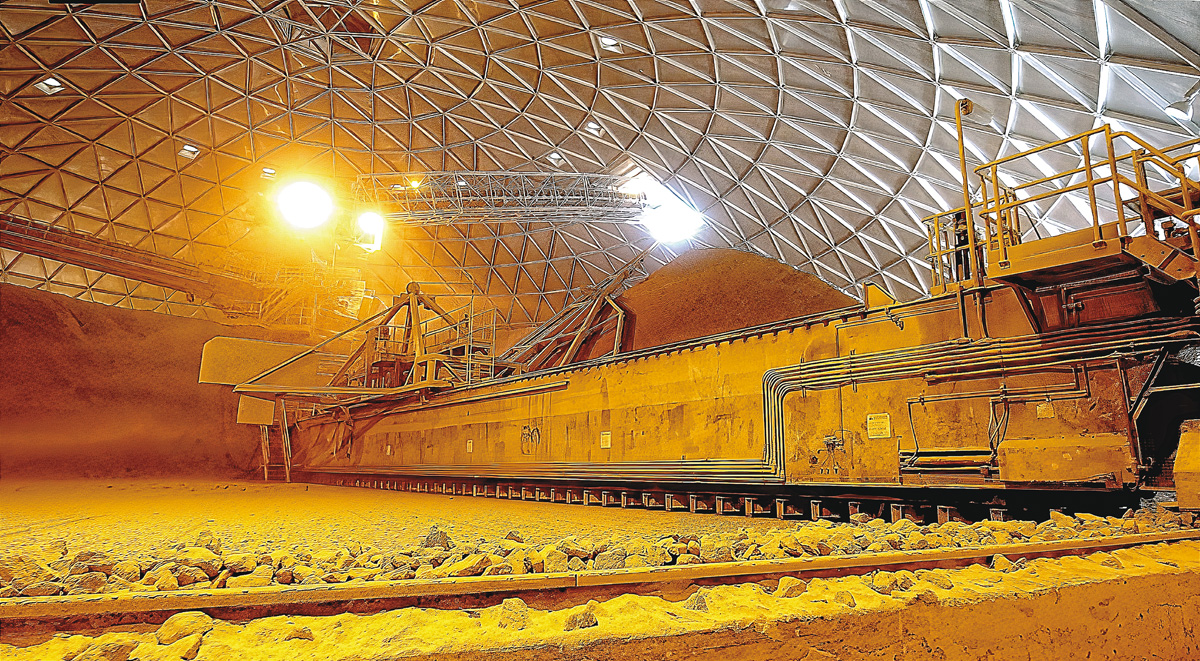
3
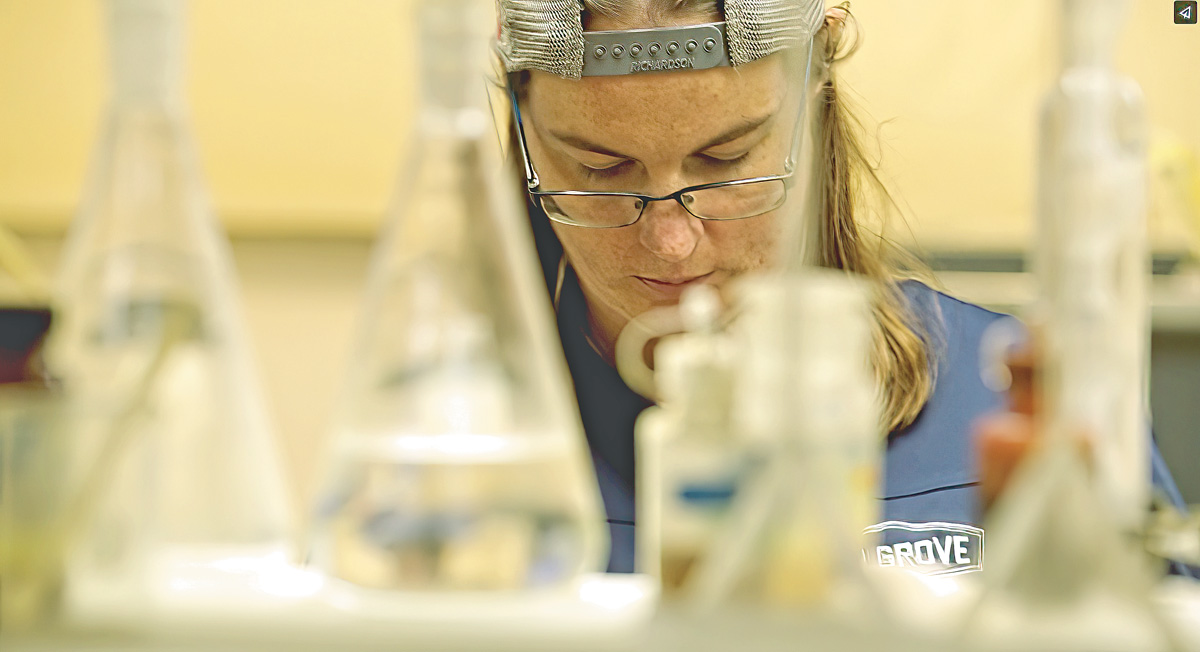
4
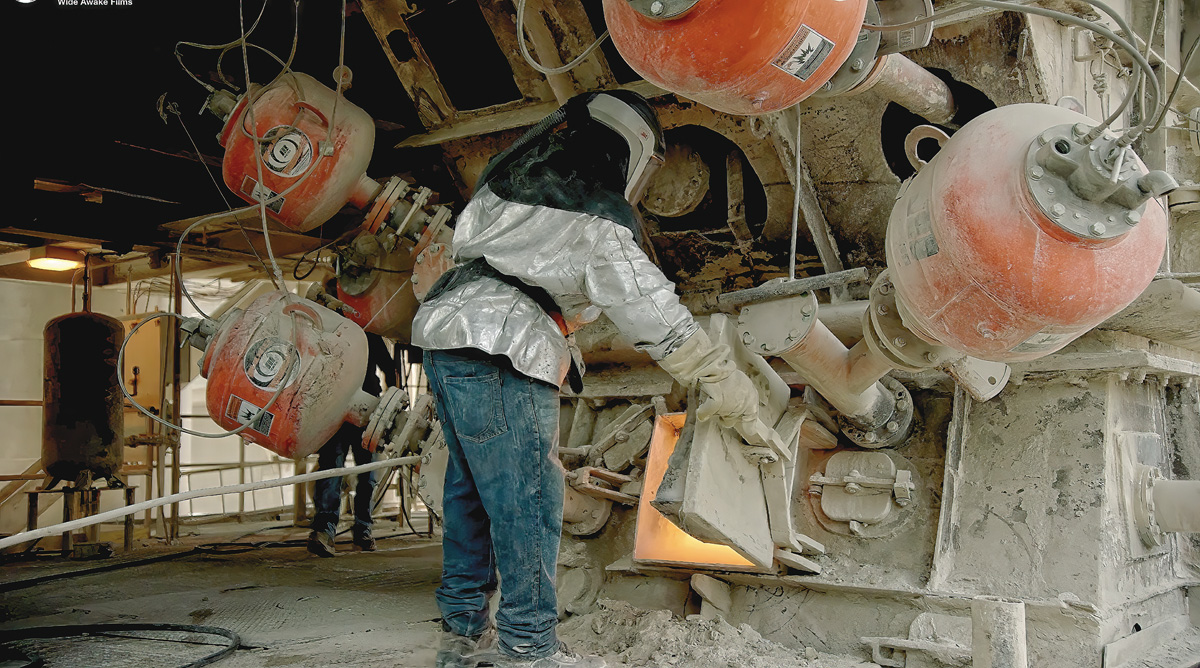
5
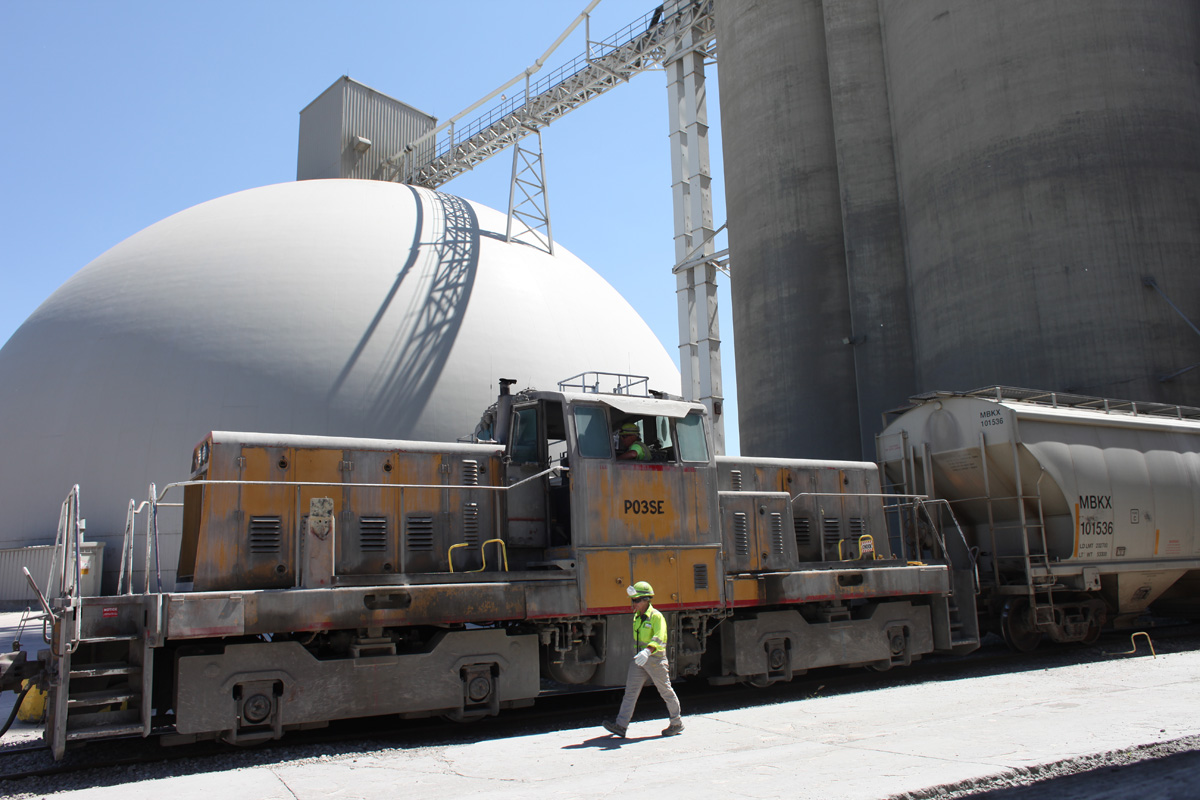