If you look around this site, the skyline’s been defined by Boilermaker work.
THERE ARE TOWNS smaller than Shell’s Pennsylvania Chemicals construction site in Beaver County, Pennsylvania. Positioned just northwest of Pittsburgh along the Ohio River, it’s one of the largest active construction sites currently in the United States. It’s hard to take it all in in a day, and it’s impossible to comprehend the scope of the project, let alone the countless individual skills of thousands of craftsmen and women steadily at work there 24/7 changing both the area’s skyline and its economy.
A little over six miles of roads as busy as any Main Street USA traverse and intersect throughout nearly 400 acres of property dotted by the ever-growing vessels, tanks, towers and other structures on their way to becoming a working ethane cracker facility. The world’s second-largest crane, affectionally known as “Mother of All Cranes,” stands sentinel among some 137 others. Villages of temporary offices, command centers, mess buildings and parking lots infill between the projects within the overall project.
At its peak, an estimated 6,000 craft professionals will be on the site, many of them represented by 15 different trade unions. And more than 300 of them are Boilermakers, mostly from Local 154 (Pittsburgh) and the National Transient Division (NTD), working for Great Arrow Builders, Bechtel, McCarl’s and Babcock & Wilcox.
“If you look around this site, the skyline’s been defined by Boilermaker work,” says L-154 steward Mark Johnson. “If you look over at the ethane cracker unit, the vessels and the towers, the quench towers or the polyethylene area, the loop reactors, the purge bins or co-gen systems—or the spheres with the tank division—our work defines this plant.”
NTD Boilermakers were the first Boilermakers to come onto the scene, settling in November 2017 to start on the plant’s 25 tanks, four spheres and one LNG tank needed for, among other things, holding fuels and sensitive substances, running the facility’s water treatment system and storing the ultimate end-product: plastic pellets that will be made into everything from cars to phone cases to food packaging.
There are 83 NTD Boilermaker tank builders on site, employed by Great Arrow Builders. Specifically, their work scope has included building three carbon steel spheres 57.5-feet in diameter; plus, an 80-foot-diameter nickel sphere for ethylene storage. The tanks consist of a double inner nickel ethylene storage tank with the inner tank measuring in at 145 x 70 feet. In the water treatment area, there are two filter water tanks, five aeration tanks, two flow equalization tanks, oil recovery and caustic tanks. And then there are 13 other myriad tanks of various sizes and type. Other work scopes coming up are furnaces’ tray tower work and all stair tower platform and structural work for the tanks and spheres.
“This type of job is really substantial for the Boilermakers,” says Shon Almond, Assistant Director of the NTDS. “With all the different styles of tanks and spheres, carbon and nickel, this project is a good view of the many styles the NTD Boilermakers tank industry has to offer.”
“This has been a great economic impact for the region and for our hall and the Boilermakers. To get a job like this that lasts three or four years, it’s great to have that. And it’s year-round employment.”
—Michael Stanton, Local 154 Business Agent
“This truly is a great project to see the wonderful craftsmanship of the Boilermakers.”
Estimations are that there will be steady Boilermaker work on the project for a couple more years. In addition to the NTD work, Boilermakers also built the plant’s cogeneration systems that will provide power for Pennsylvania Chemicals, including the two natural gas-fired combustion turbines and heat recovery steam generators (HRSG’s).
And up the road from where Boilermakers are putting water treatment tanks together and working on the elevated flare, others are busy in the ethane cracker unit area. They’re welding the convection passes on the first of seven furnaces that will eventually heat ethane gas to considerable temperatures, beginning the process of cracking the chemical bonds to produce ethylene and other byproducts.
“The bottom of the furnace is three separate boxes,” explains Boilermaker Nick Calore. “We flew up the top four boxes, and there are more pieces to go on top which we haven’t set yet that are coming in on barges.”
On the other side of the project site—literally about a mile away—still more Boilermakers are at work at the polyethylene unit area.
“I’ve been on some big projects, but nothing to this scale. Nothing this big. It just keeps building up around us.”
—Jim “Spanky” Witner, Local 154
L-154 Boilermaker Jim “Spanky” Witner describes setting the vessels on the polyethylene unit a month earlier. Each weighed about 1 million pounds and was set up using the behemoth PTC ring crane with a 720-foot boom.
“I’ve been on some big projects, but nothing to this scale. Nothing this big,” he says. “It just keeps building up around us. A lot of different things have popped up, a lot of heights we weren’t at before. It’s been exciting.”
And for L-154 Boilermakers like Witner, it’s also been conveniently close to home. It’s a short 35-minute drive for him and just 40 minutes from Local 154’s hall.
“So, it really is a local job, and it’s going to put back into the community here, especially into the Beaver County area. It’s nice to know what long-term benefits are going to be for this area monetarily and so on,” Witner says.
The glut of tradesmen and women calling Beaver County home while they work have already been a boon to local businesses and the county, which had suffered after the Pittsburgh-area steel mills, and then coal plants, shuttered. The facility is, in fact, being built on the grounds of a former smelting facility.
“This has been a great economic impact for the region and for our hall and the Boilermakers,” says L-154 Business Agent Michael Stanton. “To get a job like this that lasts three or four years, it’s great to have that. And it’s year-round employment.
“This job presented a lot of challenges, and I’m proud to say that our guys have accepted those challenges and really stepped up and answered the bell on those challenges.”
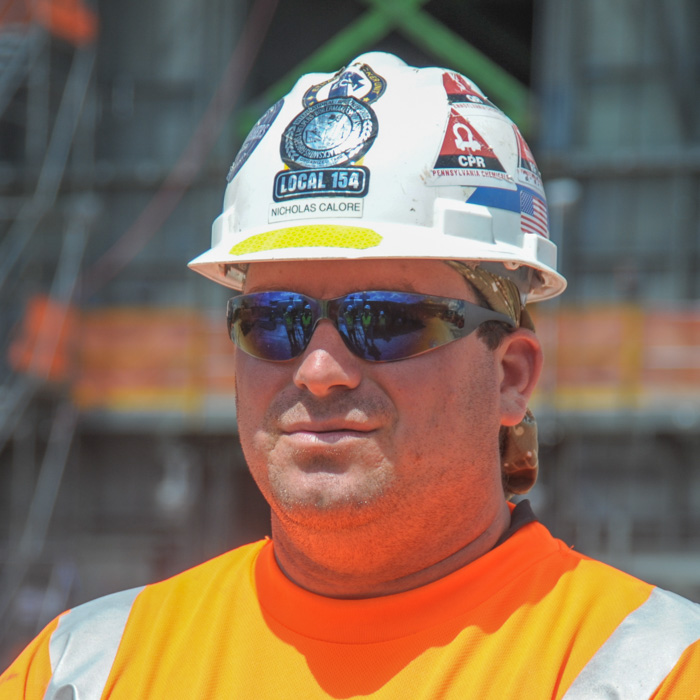
“Boilermakers have always had a strong legacy. We work really hard. We take a lot of pride in our work and do a good job, do it on time, do it right. It means a lot to me. I’m a second-generation Boilermaker so, you know, you come out here and do a good job.”
—Nick Calore, Local 154
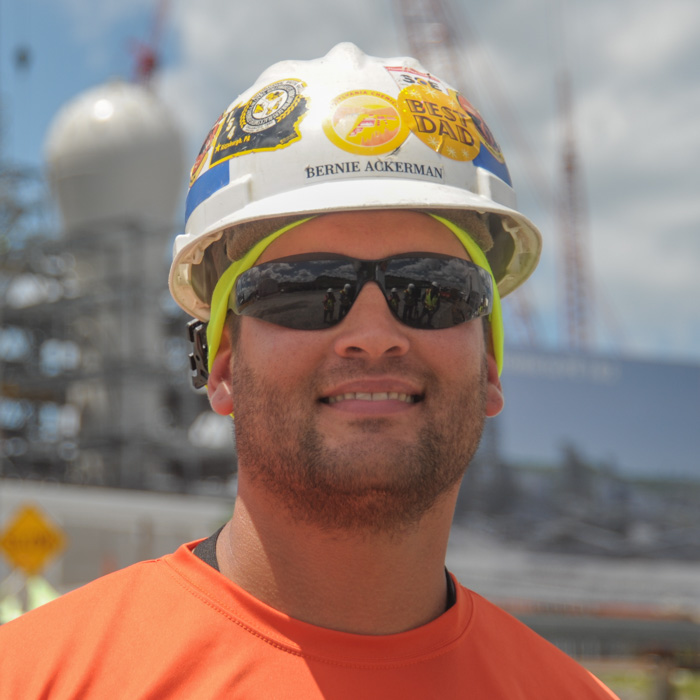
“I became a Boilermaker, because I thought the work was pretty neat. I thought it was unique, and I could have a lot of fun doing it—and I have had a lot of fun doing it over the years. I’ve met a ton of great people, been to a lot of places, and it’s been a great experience throughout my life.”
—Bernie Ackerman, Local 154
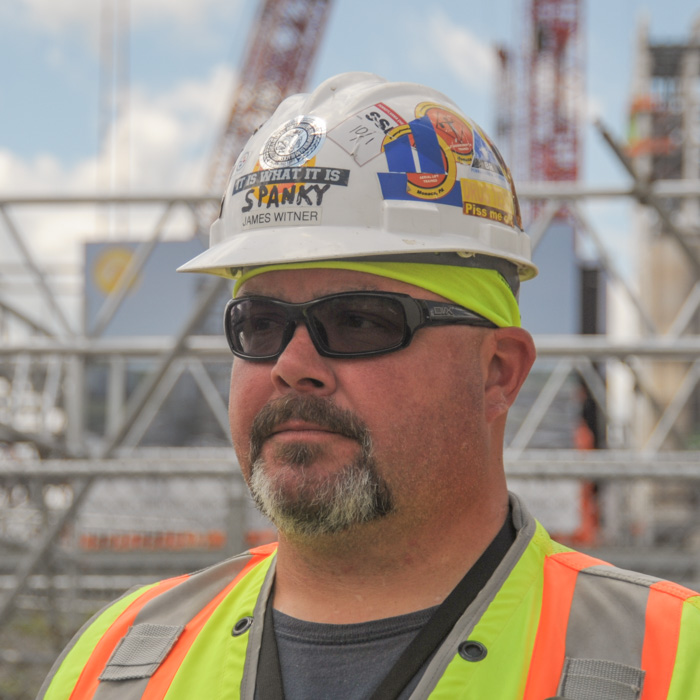
“As Boilermakers, we take pride in our work. We can do anything. If something needs done, we say, ‘We can do it. We’ll take care of it. For the big rigging, welding, we’ll do it. We’ll figure it out.’ ”
—Jim “Spanky” Witner, Local 154