ON PICTURESQUE VANCOUVER Island, down a quiet street near the water in the capitol city of Victoria, Local 191 Boilermakers (Victoria, B.C.), along with travelers, are doing their part in bringing Canadian shipbuilding back from the dead. This rebirth is taking place, in part, at Seaspan’s Victoria Shipyards, which operates within the federally-owned Esquimalt Graving Dock, the largest solid bottom commercial drydock on the West Coast of the Americas.
Local 191 is the signatory union with about one-fifth of the employees at Victoria Shipyards from the Brotherhood and the rest from other unions. IR Richard MacIntosh said work started ramping up near the end of 2017 when Victoria Shipyards secured federal contracts through the Canadian Navy and also New Zealand.
Boilermakers are currently working on frigate upgrades for New Zealand as well as a submarine retrofit for the Canadian Navy, in addition to other projects.
This renaissance is not without its challenges. The main issue is an abundance of work and high demand for qualified workers.
“Around 25 years ago, the Canadian Navy and Coast Guard stopped building ships,” said Joe O’Rourke, Vice President and General Manager of Victoria Shipyards, which currently employs around 1,100 trades men and women. “With that, the supplier and the knowledge-base of workers shifted away.”
Local 191 BM-ST Rob Taylor worked at the shipyard before his election to lodge leadership last year. He said there are only about a dozen older Boilermakers who have a complete shipbuilding skillset.
“One thing I’ve noticed with those who are coming up on retirement: There’s going to be a large discrepancy in knowledge between older members and newer ones,” he said.
That’s something Taylor is addressing with the local’s first-ever apprenticeship program, which will help train qualified workers for the shipyard.
One of the apprentices, Tori Cockerill, is a steel fabricator making parts for the submarine refit. She’s been at the shipyard two months. O’Rourke said it can take up to five years to fully train a new hire, a path Cockerill is just beginning and one she also enjoys.
“I absolutely love it here,” she said. “Everyone is so kind. It’s the best environment I’ve ever worked in.”
O’Rourke said that every person is giving his or her best on a daily basis but finding qualified people with the skills needed to finish projects is the biggest challenge at the shipyard. Seaspan submitted bids for several jobs, not expecting to be awarded all of them—and now these projects are putting a time crunch on the labor force.
“When you bid on a variety of projects you’re not supposed to win all the bids and they’re not supposed to start at the same time. This is an oddity,” O’Rourke said with a shake of his head. “We’re asking a lot, and we’re going to get there as a team with a promise that after this growth period, we’ll catch up.”
And while the cost associated with rebuilding the labor force is high right now, O’Rourke believes building and repairing in Canada is the best solution because the money spent on labour is going back into Canada.
“You should always be building your own vessels because you’re reinvesting in yourself,” he said. “It’s good for Canada and good for Seaspan.”
Submarine work at the shipyard has also required uplift in skillset over the last five years. The need for specialty and high-pressure welding, as well as steel fabrication, is in demand.
Canada has four submarines they rotate, with one sub parked in the shop for repairs. The subs require high-level maintenance work as well as computer upgrades. And it requires a lot of welding to repair hull pitting where salt water has gotten under the absorbing tiles and has corroded the hull. To fix the damage, absorbing tiles are removed before Boilermakers clad the outside of the sub.
Cladding, a process generally used to address corrosion, fits welded metal over the surface of the work as opposed to joining two pieces of material. After the welding is done, workers grind down the weld creating what looks like an entirely new surface.
“We had three tons of cladding on the hull,” O’Rourke said of a recent retrofit. “That’s a lot of weld.” In some instances, Boilermakers working on subs are welding “blind with a mirror,” using the reflection on the glass to guide them to lay the bead.
O’Rourke said that Boilermakers at the shipyard have had to evolve, but have risen to the challenge, with the quality improving with more training and more focus on weld procedures. “Boilermakers know what they’re doing and train their workforce to do it. We continue to build our workforce to attain the highest standard of weld quality,” O’Rourke said. “We’ve put millions of dollars into training in the last three or four years. Now, we have some of the finest welders in Canada.”
For Boilermakers working at Seaspan’s Victoria Shipyard, it’s more than just a job.
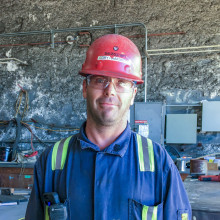
17-year Boilermaker Cory Haakonson has been at Victoria Shipyards for a year and a half and is currently working on the New Zealand frigates. He said he likes coming to work because he sees it as his contribution to world peace and freedom.
“We’re doing such a service to the free world and NATO and building things that help guarantee our freedom.”
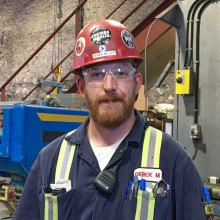
Derek Miller has been a Boilermaker 10 years and works as a welding supervisor in the submarine project. He likes the variety of work at the shipyard.
“Every day presents a new challenge and it’s interesting to see how we can overcome it.”
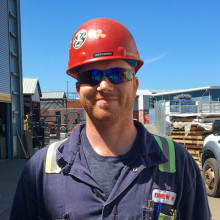
Drew Hansen has worked at the shipyard since 2006, but as a Laborer. From 2006 to 2011, the year he indentured into the Boilermakers, he had the opportunity to look around at the other trades in the shipyard before he settled on Local 191.
“I got a good chance to see how things work in all the different trades to find out what I wanted to do. I thought this looked pretty cool. I’ve always wanted to a little welding and fitting and work with steel. I had the opportunity to do an apprenticeship so I took it. I haven’t regretted it yet.”
He’s currently working on the submarines as a field department charge-hand, supervising union members and running the crew for jobs.